Augmented reality for the smart railway workshop
AI-supported assistance systems for intelligent maintenance
Mobile applications are becoming increasingly important in railway maintenance workshops, as they facilitate the maintenance of complex equipment such as a rail vehicle.
ZEDAS GmbH, software specialist for the maintenance management of railway vehicles, is already supporting its customers in the digitalisation of the workshop, towards a paperless workshop, among other things with intuitive tablet applications especially for workshop employees.
In other industries, data glasses and AI-supported assistance systems are already in use in maintenance. The practical suitability for the railway industry needs to be tested. In order to better guide maintenance staff through the maintenance process, ZEDAS GmbH is working together with BLG RailTec GmbH and the Brandenburg University of Technology Cottbus-Senftenberg in a joint research project on an augmented reality application (AR) for data glasses and tablets specifically for the railway workshop.
With the AR application, it is possible to relate a wagon in the workshop and an order from the asset management system in three dimensions. This means that the corresponding work area on the wagon is marked for the maintenance task, arrows show the correct position of the next component to be worked on and drawings, documents, photos and videos are displayed in context.
Webinar
Mobile Assistance Systems in Railway Maintenance
In the online seminar, we show you how to use specific assistance systems and mobile apps to significantly simplify maintenance and documentation.
When the wagon arrives at the workshop, the wagon number recognition system based on artificial intelligence takes over the unique identification. Existing orders, faults and checkpoints are displayed directly on the screen section with the wagon via AR. In this way, the maintenance technician knows immediately for which components there are orders. He is supported by checklists, instruction videos and documents when carrying out maintenance measures.
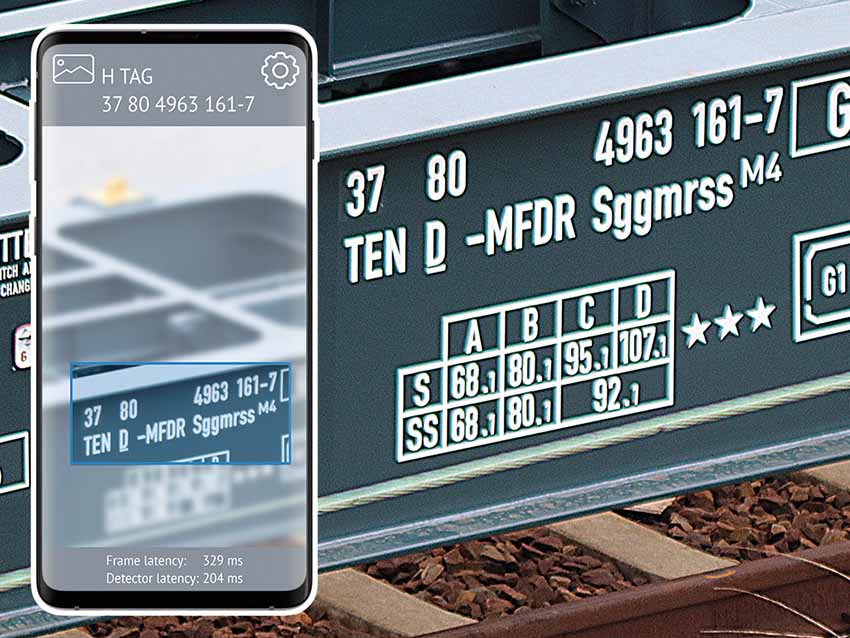
High process safety
There are high safety standards in the railway sector. Through guided maintenance, the digital assistance system guarantees that the workshop employee is specifically informed about safety-relevant components. Only when he has read the instructions for the work step, the next work steps are enabled. In addition, the notes and process information can be updated easily and centrally - the workshop employees are always up to date.
Clearly defined workflows give the maintenance staff exactly the sequence and the positions at which they have to carry out the work steps. He is guided step by step from component to component and receives visual instructions. The AR application also displays the measured values, limit values or circuit diagrams of the components to be processed. Furthermore, the associated maintenance plans can be viewed: in this way, the maintenance technician can also carry out the maintenance that is due in the near future when rectifying a malfunction. Augmented reality helps to increase the reliability of service and maintenance processes and reduce the risk of errors.
Time savings through automated, immediate ECM-compliant documentation
Which jobs have been completed? Which ones were started? Which operating resources were used and which in-house materials were consumed? In many railway workshops today, this is filled out on paper by the maintenance staff and then has to be extensively digitised and archived by office staff so that all proofs are available in an ECM-compliant form in the event of an official inspection.
Digital documentation is different: the workshop employee simply documents work steps, measured values and the like by voice command or tablet in parallel during maintenance, because the digital assistant is always with him. The immediate, digital documentation alone saves a lot of time and avoids errors. This creates uniform, person-independent protocols that are available in real time in the main system for archiving, for authorities or for the end customer during contract work.
Securing and making knowledge available
It is a challenge when experienced employees retire or leave the company for other reasons. Much of the knowledge goes with these employees.
The augmented reality application can mitigate this loss somewhat because it acts as a knowledge repository that supports new and external employees in particular. Experienced employees store their knowledge of process steps in the central database and show how certain maintenance processes are best carried out. This creates a reference manual that can be implemented later by other employees, but also further optimised. If the instructions and documentation are only saved in paper form, it is difficult to always provide all employees with the latest version. After all, who can ensure that no old versions are in circulation?
But how is the knowledge store filled? The knowledge store is fed from two sources: the main system zedas®asset, which is a railway-specific CMMS (short for Computerised Maintenance Management System, which helps to manage assets, plan maintenance work and track work orders) and the editorial documentation. In the best case, the recordings for the documentation are simply made in parallel during maintenance. In the process, maintenance activities are also documented and recommendations for action are stored, which only take place infrequently or are only carried out by individual persons or in individual workshops.
Book your software demo
Take the chance and book your software demo. Which functions are you interested in and which goals do you want to achieve with zedas®. We will be happy to help you and arrange a desired date with you.
Book a software demo nowShortage of skilled workers
Maintenance staff who specialise in certain series of rail vehicles can more easily switch to other series. Shortages of skilled workers can be mitigated by assistance systems. They can support new or less well-trained employees or subcontractors who are less familiar with certain components. Especially for young employees, the workplace is more attractive with new technologies. Here, an intuitive, simple user interface with few buttons and short instructions is essential so that both trained and untrained employees accept and work with this digital assistant.
What are the advantages of augmented reality applications?
Defined workflows ensure processes that follow a continuous, everlasting concept. This makes it possible to control the use of components and personnel much more efficiently and to achieve the greatest possible economic success. In addition, the use of augmented reality can be used for the induction of new employees or for training. But long-serving employees can also use these applications for training and instruction in new processes or series. With the help of checklists, in-house processes can also be covered and the quality of the work can thus be ensured across the board in other maintenance centres.
CONCLUSION
The aim of the zedas® AR applications is to improve the quality of work and also safety with the help of augmented reality. Depending on the situation and object, information is displayed to the user where it is needed: Directly in the field of vision and on the object in question.
The goals of the research project are: the development of an AI-based repair assistance system to secure knowledge, which can simultaneously take over the qualification of specialist and non-industry personnel, the establishment of an attractive employer image and the development of SMEs, via the digitalisation of their processes and the use of AR/VR systems, into an efficiently and innovatively working interface between society and industry. In this way, it aims at technical, especially AI-based, but above all also economic and social innovations.